
While VISI automatically picks the mold base when the insert and part are complete, he is particularly impressed with the speed and accuracy it can be manually tailored if required. Once he is happy with the split he subtracts the part out of the inserts and establishes the insert size around it. “I make either the fixed half or moving half transparent onscreen, so I can look inside and ensure the faces are touching, and that everything fits and works properly.” As VISI has a large library of materials with all their specs and characteristics it’s simple to apply shrinkage to the particular plastic I’m working with.”Īnd he says core and cavity separation is quick and easy, even with varied split lines, as are sliding block and tricky shot out areas. “I check the features with the draft analysis function, making sure it has relevant draft tapers, and then move on to the design. It’s got a variety of tools to ensure that all surfaces meet up, because if we’re trying to work with a poorly designed model, the mold tool won’t work. “A big advantage of VISI is that we can check the model’s integrity before we start.

He says their process begins with the plastic component – whether they are producing the tool for another molder, or to run on their own molding machines. Using the Hurco machines and VISI means that in terms of design and cutting the forms, we save at least half the time…and the overall time taken to produce the complete tool is reduced by around a third.”
#Manual pdf vero visi software#
“Every mold we manufacture goes through both software packages. The combination of mold design with VISI, and WORKNC driving a 3-axis Hurco VMX machining center along with a Hurco Hawk and XYZ bed mills, means that everything Sharnold produces is within the required tolerances…sometimes down to + or – 0.05 of a mm. VISI has speeded up the whole design process considerably.” For example, producing split lines is much easier, as is slide generation. It’s now simple to achieve aspects that we struggled with before. “CAD designers are producing increasingly more complex parts, but VISI gives us the ability to meet those demands quickly and easily. “It’s already proving to be vital for us,” says Mark Chapman. While they have used WORKNC, from Vero Software, to machine their molds for at least 15 years, VISI…also from the Vero stable…is a relatively new investment. The machines mean the company has a locking force of between 22 and 100 tonnes, giving them the ability to supply molded plastic parts up to 230 grams. While making tools for plastic injection molders remains an important part of their business, they set up their own molding operation in 2000, and now have seven molding machines – two Boys, two Battenfelds and three Arburgs.

Maurice bought into the business in 1982, eventually taking sole ownership. Nowadays it is run by just four people: Maurice Chapman, his two sons Mark and Stephen, and Stephen’s wife Tracy. The company was established as a subcontract mold maker in 1957, moving to their current 3,500 square foot premises in Northamptonshire, in 1970 with ten employees. Mark Chapman, Company Secretary and Moldmaker Designing their molds in VISI, and machining them with toolpaths generated by WORKNC, ensures that the tight tolerances they need to achieve are met first time, every time.
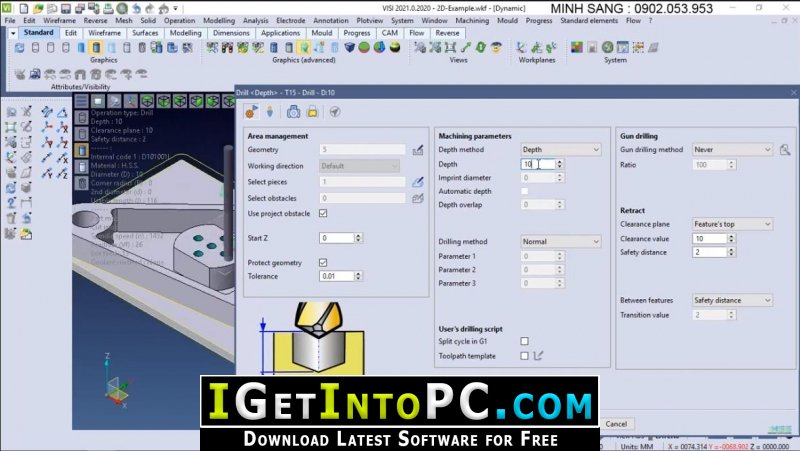
Those are the words of Mark Chapman, company secretary and moldmaker at family-run business Sharnold Ltd. But when we invested in VISI that immediately came down to a couple of days. “Some complex mold tools used to take me nearly a week to design.
#Manual pdf vero visi code#
– And WORKNC Machining Code Is Ready In Moments
